In FR SERVICIOS LOGISTICOS we take care of your stock management, so you may see its status and all information related to it at all times, thus enabling you to forecast your supply, sales and obsolescence requirements.
Our stock management processes encompass all stock-related processes and information and are necessary to control and organise the flow of goods in the warehouse. For this reason, we also include actions for location assignment, traceability and stock reliability, replacement organisation and the consolidation of goods, respecting LIFO, FIFO and FEFO control strategies, among others.
The necessary stock control provides a highly detailed, real-time picture of the stock in the warehouse at any given time, and includes all information related to the quantity, characteristics and location of each product. The reliability of this record is fundamental for preventing errors that interfere in warehouse activity and sales to customers.
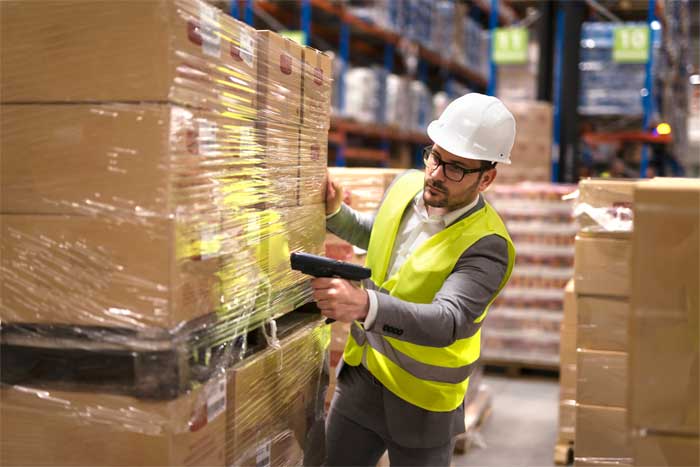
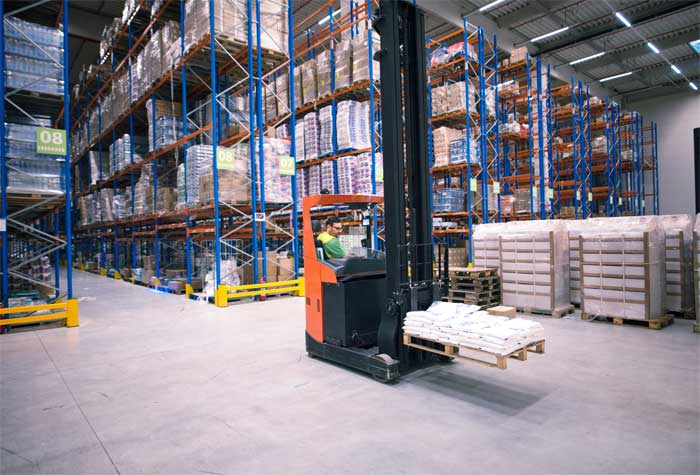
Our perpetual inventory adjustment processes make ongoing checks between theoretical stock and real stock each time an operator accesses a location to interact with this stock. In this way, the inventory is kept updated at all times to ensure that your customers’ product service is not affected.
We have the most efficient IT tools to optimise inventory, thus proactively providing the necessary information to improve the productivity of stored stock. Analysing the data related to stored products means that their location can be improved by positioning them in the most suitable areas of the warehouse. Data analysis also improves the efficiency of the movements necessary to offer the service, establish semi-obsolete products and act with them.
Our stock and inventory management processes:
- Exclusive area in the warehouse for your goods.
- Area divided into sectors according to:
- Product families
- Stock turnover
- Type, volume and weight of the product storage units
- Picking processes
- Sales markets
- Control of the degree of occupation in the area and sectors.
- Recalculations of product turnover (A-B-C).
- Pallet consolidation to save space.
- Goods flow processes and the size of picking locations in the warehouse that depend on each product’s turnover.
- Real-time information about the stock, including the following details:
- Items reserved for portfolio sales
- Items blocked from selling due to quality processes, defects, quarantine, etc.
- Items available for sale
- Automated stock reports in comparison with the declared minimum and maximum stock.
- Automated reports of unsold products during a defined period.
- Perpetual inventories made during the development of the processes that interact with the stock.
- Planned cycle stock inventory.
- Annual extraordinary inventories validated by external audits for the inventory statement at the closure of the financial year.